Environmental
Sustainability
PRODUCT
OEKO-TEX® MADE IN GREEN
We were one of the first mattress and pillow brands to receive the OEKO-TEX® MADE IN GREEN label on our products. Our TEMPUR PRO®, TEMPUR PRO Air™, TEMPUR Prima®, TEMPUR One™ & TEMPUR FORM™ mattresses & toppers, and TEMPUR® Comfort Pillow ranges are all OEKO-TEX® MADE IN GREEN labelled. This ensures every labelled product is made with materials thoroughly tested to be free from harmful substances and produced in environmentally friendly facilities under socially responsible working conditions.
You can see where our OEKO-TEX® MADE IN GREEN labelled products are made, including the country of origin for textile and cover production. Simply enter the relevant product ID code into the OEKO-TEX® website or scan the relevant QR code on your mattress or pillow cover
Please visit tempur.com to see which of our products use the MADE IN GREEN label.
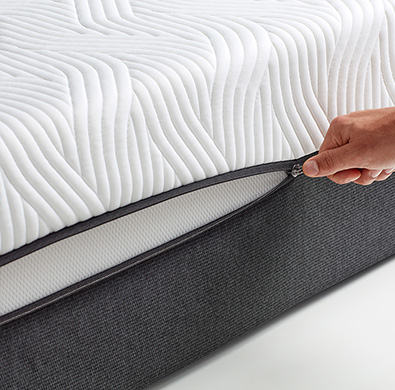
We’re increasing the emphasis on sustainability within our product development process by exploring methods to integrate additional sustainable components, supply chains and methods of assembly into our products.
Our products already meet strict certification standards such as OEKO-TEX® Standard 100 and TÜV Rheinland Certified, which ensure that our products are tested for harmful substances and pose minimum risk to human health.
In our Danish production facility, our management systems are certified according to ISO 9001 (quality), ISO 14001 (Environment), ISO 45001 (Health and Safety), ISO 50001 (Energy) and OEKO-TEX® STeP.
PACKAGING
We continuously look to re-develop the packaging of our products to reduce the amount of new materials and increase the amount of recycled materials used. Internationally, our cardboard packaging for TEMPUR® products is made from up to 78% recycled fibers from our FSC certified supplier and can be recycled. In 2022, we changed to foil packaging that is 100% recyclable and made from at least 50% recycled material for all our mattresses produced at our manufacturing facility in Denmark. We are looking at expanding the use of this foil to additional product categories manufactured at this facility.
CARBON NEUTRAL by 2040
GOAL: We are committed to achieving carbon neutrality in our global wholly owned operations by 2040
Our objective is to reduce or offset 100% of Scope 1 and 2 greenhouse gas emissions from our wholly owned manufacturing, retail, and logistics operations by 2040. Scope 1 emissions are those that come directly from our operations, and Scope 2 emissions are those that come from the energy we buy to power our operations. We plan to achieve carbon neutrality through absolute Scope 1 and Scope 2 emission reductions from the continued use of renewable energy and operational efficiency improvements, and the use of carbon capture initiatives.
RESOURCE CONSERVATION
GOAL: Source 100% of renewable electricity for our US and European manufacturing operations by 2040
PROGRESS TO DATE:
100% of our wholly owned global manufacturing and logistics facilities electricity needs were powered by renewable energy in the twelve month period ending September 30, 2023. Our TEMPUR® UK head office has been sourcing 100% of its electricity from renewable sources since July 2021.
Solar energy generated by our solar panels at our production facility combined with our sourced energy from a solar park is expected to result in over 80% of our Danish operations being powered by solar energy in future years.
Through pursuing environmental certifications, our processes and products are audited and validated by independent third parties.
This ensures the integrity of our operations and consistency across our manufacturing and logistics management systems.
As an example, our Danish production factory is ISO 50001 certified – this is an international standard which recognises businesses who have taken steps to enhance their energy performance.
As part of our energy management system, we have implemented energy-saving LED lighting and motion sensors, reducing our energy consumption and increasing energy efficiency.
In the twelve month period ending September 30, 2023, our Danish facility expanded their LED lighting utilization from 44% to 70%.
WASTE MANAGEMENT
GOAL: Zero Waste to Landfill for manufacturing sites, corporate offices and R&D labs worldwide by 2025
We are committed to reducing waste through recycling and waste minimization efforts across our global operations. To ensure progress is monitored effectively, we meticulously track waste generated during production, and use an internal reporting system for continuous assessment.
Our manufacturing facility in Denmark has achieved zero waste going to landfill, and is recycling over 60% of all waste, with the rest going to energy recovery. There has also been zero landfill waste from TEMPUR® UK warehouse and distribution operations since 2019.
END OF LIFE
Longevity is at the heart of what we do. All TEMPUR® mattresses have a 10-year guarantee, tested to our rigorous standards to give you years of true, restful sleep. You can replace the top cover of your mattress to give it a new lease of life.
When it comes to disposal, TEMPUR® mattress and pillow covers are easily removeable for recycling, with the foam core being recycled separately*
When our mattresses reach their end of life, the core material can be cleaned and shredded for use in new products, such as carpet underlay, insulation panels, car seats and boxing pads.
In Europe, many of the countries in which we operate have implemented schemes relating to product lifecycles in which mattress manufacturers support the funding of recycling end-of-life mattresses. We are tracking the development of similar schemes across our global markets, not only those which will become legally required but also joining voluntary local schemes.
And, we are continuously searching for more ways to reuse and recycle our unique material, for example, in our work with industry and research partners on the PURfection project.
We are working around the globe to identify regional recycling opportunities for returned products, and will continue to work with our distribution partners to increase the recycling of these products.
*Please check with your local authority on waste disposal information.